Quartz Crusher
- Jaw Crusher
- Primary Crushing: Ideal for coarse crushing of large quartz blocks (input size: 150–350 mm).
- Output Size: 10–100 mm.
- Benefits: High efficiency, low maintenance.
- Cone Crusher
- Secondary Crushing: Produces finer particles (5–50 mm) for high-purity applications like semiconductor manufacturing.
- Advantages: Precise control over output size, reduced dust generation.
- Impact Crusher
- Versatile Crushing: Suitable for medium-hardness quartz. Delivers cubical-shaped grains for construction aggregates.
- Use Case: Crushing quartz for concrete or road base layers.
- Hammer Crusher
- Cost-Effective: Best for small-scale operations or soft quartz varieties.
- Output: Powder or granules (0–5 mm).
- Increased Efficiency: Automates the crushing process, reducing manual labor.
- High Purity Output: Minimizes contamination for electronics-grade quartz.
- Cost Savings: Recycles quartz waste into valuable materials.
- Durability: Built with wear-resistant materials like manganese steel.
- Glass Manufacturing
- Crushed quartz is melted to produce glass products.
- Electronics
- High-purity quartz is used in silicon wafers and solar panels.
- Construction
- Quartz aggregates strengthen concrete and asphalt.
- Gemstone Processing
- Crushing raw quartz for jewelry or decorative stones.
- Material Hardness
- For hard quartz, prioritize jaw or cone crusher.
- Production Capacity
- Small-scale projects: Hammer crusher (1–5 t/h).
- Large mines: Cone crusher (50–500 t/h).
- Output Size Requirements
- Fine powders (e.g., 0.1 mm) require vertical shaft impactors or ball mills.
- Energy Efficiency
- Electric crusher reduce operational costs vs. diesel models.
- Brand Reliability
- Trusted manufacturers: Sandvik, Terex, Komatsu.
- Regular Lubrication: Extend bearing life with high-temperature grease.
- Wear Parts Replacement: Monitor jaw plates, liners, and hammers for wear.
- Dust Control: Install bag filters or water sprays to protect workers.
- Operator Training: Ensure safe handling of abrasive materials.
- AI-Driven Automation: Real-time adjustments for optimal crushing performance.
- Eco-Friendly Designs: Solar-powered crusher for remote mining sites.
- Modular Systems: Compact crusher for small-scale or mobile operations.
Introduction to Quartz Crusher
Quartz, a hard mineral with a Mohs hardness of 7, is widely used in glassmaking, electronics, and construction. Crushing raw quartz into usable sizes requires specialized equipment like quartz crusher. These machines break down large quartz rocks into smaller granules or powders, enabling efficient processing for industrial applications.
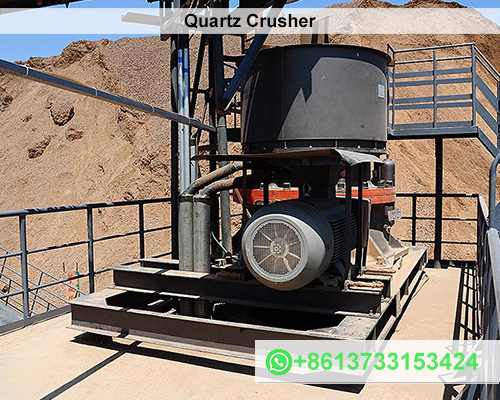
Types of Quartz Crusher
Key Benefits of Using a Quartz Crusher
Applications of Crushed Quartz
How to Choose the Right Quartz Crusher
Maintenance Tips for Quartz Crusher
Case Study: Optimizing Quartz Processing in a Mining Facility
A quartz mine in Brazil upgraded to a Sandvik CH660 cone crusher, achieving a 30% increase in output purity while reducing energy consumption by 15%. The recycled quartz is now used in premium solar panel production.
Future Trends in Quartz Crushing Technology
Conclusion
A quartz crusher is essential for transforming raw quartz into high-value industrial materials. By selecting the right type of crusher, prioritizing maintenance, and adopting advanced technologies, businesses can maximize productivity and meet growing demand in sectors like renewable energy and construction.