
SMP Modular Crushing Plant
The SMP Modular Crushing Plant combines innovation with practicality, offering a turnkey solution for industries requiring mobility, adaptability, and high-performance crushing capabilities.Capacity:70-425TPH
Application: Quarries, metallurgical mines, construction materials, highways, railways, water conservancy, chemical industries, and more. Mainly used for crushing, screening and reshaping of various stone materials and building wastes.
Chat online Call WhatsAppThe SMP Modular Crushing Plant (Standard Modular Processing Plant) is a pre-engineered, customizable crushing and screening system designed for efficiency, flexibility, and rapid deployment. It integrates primary, secondary, and tertiary crushing stages, along with screening and conveying modules, into a cohesive unit. Suitable for mining, quarrying, and construction projects, the SMP Modular Crushing Plant is engineered to handle various materials, including aggregates, ores, and recycled concrete, delivering high throughput and consistent performance.
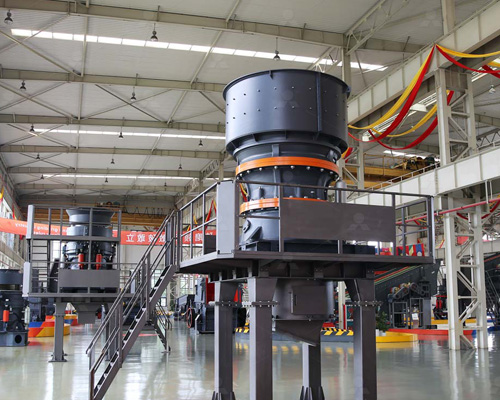
Key Features of SMP Modular Crushing Plant
- Modular Design
- Composed of prefabricated modules (crushers, screens, conveyors, control systems) that can be easily transported and assembled on-site.
- Reduces installation time and logistical challenges compared to traditional fixed plants.
- Quick Deployment
- Pre-assembled components enable rapid commissioning, minimizing downtime and accelerating project timelines.
- Ideal for temporary or remote operations where speed is critical.
- Scalability & Flexibility
- Modules can be reconfigured or expanded to meet changing production demands or material specifications.
- Supports multiple crushing stages (jaw, cone, impact crushers) and screening options for tailored solutions.
- High Efficiency
- Optimized layout reduces material transfer distances, enhancing energy efficiency and throughput.
- Advanced automation systems ensure precise control over particle size and product quality.
- Compact Footprint
- Space-saving design adapts to constrained or uneven terrains, reducing site preparation costs.
- Eco-Friendly Operation
- Dust suppression systems and noise-reduction technologies minimize environmental impact.
- Energy-efficient motors and renewable energy compatibility support sustainable practices.
- Low Maintenance
- Robust construction with wear-resistant components ensures durability and reduces lifecycle costs.
- Easy access for maintenance and repairs due to modular component design.
- Cost-Effective
- Lower capital and operational expenses compared to traditional stationary plants.
- Reduced labor requirements due to automated processes and centralized control.
- Adaptability to Harsh Conditions
- Designed to operate reliably in extreme temperatures, high altitudes, or corrosive environments.
- Integrated Control System
- Centralized PLC (Programmable Logic Controller) or touchscreen interface enables real-time monitoring, diagnostics, and remote management.
Applications
- Aggregate production for road construction and concrete.
- Mining and mineral processing (iron ore, gold, copper).
- Recycling of construction and demolition waste.
- Portable crushing for infrastructure projects in remote areas.