Pebble Crusher
- Jaw Crusher
- Primary Crushing: Ideal for large pebbles (up to 1,500 mm).
- Output Size: 50–200 mm.
- Benefits: High throughput, simple maintenance.
- Cone Crusher
- Secondary/Tertiary Crushing: Produces finer, cubical-shaped particles (5–50 mm).
- Advantages: Precise control, energy-efficient for hard pebbles.
- Impact Crusher
- Versatile Crushing: Suitable for medium-hard pebbles. Creates uniform gravel for landscaping.
- Use Case: Ideal for producing decorative stones or road base materials.
- Vertical Shaft Impactor (VSI)
- Fine Crushing: Generates sand-sized particles (0–5 mm) for concrete mixing.
- Eco-Friendly: Reduces the need for natural sand extraction.
- Cost Savings: Converts raw pebbles into valuable aggregates, reducing material procurement costs.
- Sustainability: Recycles natural resources and minimizes waste.
- Customizable Output: Adjust settings to meet specific size requirements for construction or landscaping.
- Durability: Built with wear-resistant alloys to withstand abrasive pebbles.
- Construction
- Base layers for roads, driveways, and concrete mixes.
- Landscaping
- Decorative gravel for gardens, pathways, and water features.
- Erosion Control
- Stabilizes slopes and riverbanks.
- Industrial Uses
- Filter media in water treatment plants.
- Material Hardness
- Hard pebbles (e.g., granite) require cone or jaw crusher; softer stones work with impact crusher.
- Production Capacity
- Small projects: 10–50 t/h (e.g., mobile crusher).
- Large quarries: 100–500 t/h (e.g., stationary cone crusher).
- Mobility Needs
- Tracked or wheeled mobile crusher for on-site processing.
- Energy Efficiency
- Electric models lower operational costs compared to diesel-powered units.
- Brand Reputation
- Trusted manufacturers: Metso, Sandvik, Terex, McCloskey.
- Regular Inspections: Check jaw plates, liners, and bearings for wear.
- Lubrication: Use high-performance grease to extend component life.
- Dust Management: Install water sprays or dust collectors to protect operators.
- Operator Training: Ensure safe handling of abrasive materials.
- Hybrid Power Systems: Solar-diesel hybrids for remote operations.
- Smart Automation: IoT-enabled crusher for real-time performance monitoring.
- Modular Designs: Compact, portable units for small-scale projects.
Introduction to Pebble Crusher
Pebbles, naturally rounded stones found in riverbeds and coastal areas, are widely used in construction, landscaping, and road building. A pebble crusher is a specialized machine designed to break these hard, abrasive rocks into smaller, uniform sizes for industrial applications. Whether you’re processing aggregates for concrete or creating decorative gravel, choosing the right crusher is critical for efficiency and cost-effectiveness.
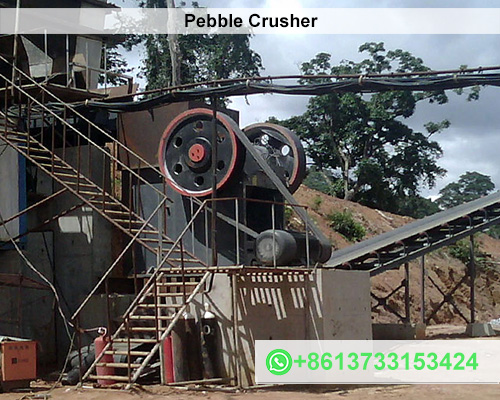
Types of Pebble Crusher
Key Benefits of Using a Pebble Crusher
Applications of Crushed Pebbles
How to Choose the Right Pebble Crusher
Maintenance Tips for Pebble Crusher
Case Study: Boosting Efficiency in a River Pebble Quarry
A quarry in New Zealand replaced its outdated hammer crusher with a Metso Nordberg HP300 cone crusher, achieving a 40% increase in production efficiency. The crushed pebbles are now used in high-demand landscaping projects across the region, reducing reliance on imported materials.
Future Trends in Pebble Crushing Technology
Conclusion
A pebble crusher is a vital investment for industries relying on high-quality aggregates. By selecting the right machine, prioritizing maintenance, and adopting innovative technologies, businesses can enhance productivity, reduce costs, and contribute to sustainable resource management.