400-600 TPH River Stone Mobile Crushing Plant In Ethiopia
- Equipment Configuration
- Primary Crusher: Jaw Crusher (PE-1200×1500) – Handles large river stones up to 1,000mm.
- Secondary Crusher: Cone Crusher (HPT-300) – Produces uniformly shaped aggregates.
- Tertiary Crusher: Vertical Shaft Impact Crusher (VSI-1140) – Enhances cubical particle shape for high-quality concrete.
- Vibrating Screens: 3-layer screens (3YK-3070) for precise grading.
- Conveyor System: 15-meter extendable belts for flexible material transfer.
- Mobility and Adaptability
- Track-mounted design allows easy relocation across rugged Ethiopian terrain.
- Diesel-electric hybrid power ensures operations in areas with unstable grid electricity.
- Automation and Safety
- PLC control system monitors performance and reduces manual intervention.
- Emergency stop functions and dust suppression systems comply with ISO safety standards.
- Cost Efficiency
- Eliminates transportation of raw materials to stationary plants, saving 15–15–15–20 per ton in logistics.
- Processes 400–600 TPH, reducing project timelines by 30–40%.
- Environmental Compliance
- Low-noise motors and water-spray systems minimize dust and noise pollution.
- Recycled water usage aligns with Ethiopia’s green construction policies.
- Durability in Harsh Conditions
- Reinforced steel frames withstand abrasive river stone.
- Weather-resistant components ensure uptime during rainy seasons.
- Challenge: Supplying 500,000 tons of aggregates for the Addis Ababa–Djibouti railway extension.
- Solution: Deployed the mobile plant near the Awash River, processing river stone directly on-site.
- Results:
- Achieved 550 TPH average output.
- Reduced fuel costs by 25% with hybrid power mode.
- Delivered aggregates within 8 months, accelerating the railway’s completion.
- Material Testing
- Conduct hardness and abrasiveness tests to select the right crusher liners (e.g., manganese steel).
- Maintenance Plan
- Replace wear parts (jaw plates, cone mantles) every 400–500 operating hours.
- Schedule daily inspections of hydraulic systems and belts.
- Operator Training
- Train staff to adjust crusher settings based on feed size and moisture content.
- Initial Investment: 800,000–800,000–800,000–1.2 million (depending on configuration).
- Operational Cost: 12–12–12–18 per ton (includes fuel, labor, and maintenance).
- ROI Timeline: 12–18 months for large-scale infrastructure projects.
Introduction
Ethiopia’s rapid infrastructure growth demands efficient solutions for aggregate production. A 400-600 TPH (tons per hour) river stone mobile crushing plant has emerged as a game-changer, enabling on-site processing of raw materials for roads, bridges, and urban projects. This article explores the design, operational advantages, and real-world success of this mobile crushing system in Ethiopia’s challenging terrain.
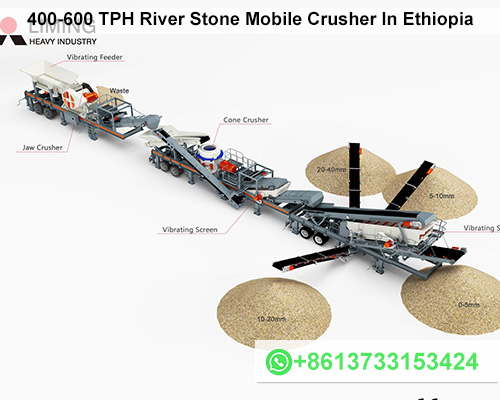
Project Overview: Crushing River Stone in Ethiopia
Location: Addis Ababa and Oromia regions, Ethiopia
Material Processed: River stone (hardness: 5–7 Mohs)
Output Requirements: 0–5mm, 5–20mm, 20–40mm aggregates
Primary Use: Road base layers, concrete production, and railway ballast
Key Features of the 400-600 TPH Mobile Crushing Plant
Why This Mobile Plant Succeeds in Ethiopia
Case Study: Crushing Plant in the Oromia Region
How to Optimize a Mobile Crushing Plant for River Stone
Cost Breakdown and ROI
Conclusion
The 400-600 TPH river stone mobile crushing plant is a cornerstone of Ethiopia’s infrastructure development, offering unmatched flexibility, efficiency, and sustainability. By integrating advanced crushing technology with rugged mobility, Ethiopian contractors can meet rising material demands while adhering to environmental and budgetary goals.