Iron Ore Stone Crushing Line
- Primary Jaw Crusher
- Model Example: Liming C6X Series Jaw Crusher
- Role: Coarsely crushes raw iron ore (≤1,500 mm) into 150–300 mm chunks.
- Features: High crushing ratio, reinforced structure for abrasive materials.
- Secondary Cone Crusher
- Model Example: Liming HPT Multi-Cylinder Hydraulic Cone Crusher
- Role: Further reduces ore to 20–50 mm for efficient grinding.
- Advantages: Automatic overload protection, energy-efficient operation.
- Tertiary Impact Crusher (Optional)
- Model Example: Liming VSI6X Sand Maker
- Role: Produces finely crushed ore (≤10 mm) for pelletizing or direct shipping.
- Benefits: Cubical output shape, low dust generation.
- Vibrating Screens and Feeders
- Model Example: Liming S5X Vibrating Screen
- Role: Classifies crushed ore into precise size fractions.
- High Efficiency & Durability
- Liming’s crusher use high-manganese steel components and advanced hydraulic systems to withstand iron ore’s abrasiveness, reducing downtime by 30%.
- Energy Savings
- Intelligent automation and optimized motor designs cut power consumption by 15–25% compared to conventional systems.
- Customized Solutions
- Liming engineers design crushing lines tailored to your ore type (e.g., magnetite, hematite), capacity (50–2,000 t/h), and site conditions.
- Eco-Friendly Operations
- Integrated dust suppression and noise reduction systems ensure compliance with environmental regulations.
- Blasting & Loading
- Raw iron ore is extracted and transported to the primary crusher.
- Primary Crushing
- Liming C6X Jaw Crusher breaks down large ore blocks into manageable sizes.
- Secondary Crushing
- Liming HPT Cone Crusher further reduces the ore for grinding readiness.
- Screening & Grading
- Liming S5X Vibrating Screen separates ore into commercial grades (e.g., lump, fines).
- Stockpiling & Transport
- Final product is stored or shipped for downstream processing.
- Preventive Maintenance
- Regular inspection of Liming crusher wear parts (e.g., jaw plates, mantles) extends equipment lifespan.
- Automated Control Systems
- Liming’s Intelligent Crushing Control System adjusts feed rates and crusher settings in real time to optimize output.
- Modular Design
- Liming’s portable crushing plants reduce infrastructure costs for remote mining sites.
- 25% increase in throughput (to 800 t/h).
- 18% reduction in energy costs.
- Zero downtime due to Liming’s 24/7 remote technical support.
- AI-Driven Predictive Maintenance: Liming’s IoT-enabled crusher predict component wear, reducing unplanned shutdowns.
- Hybrid Power Systems: Solar-diesel hybrid units for off-grid mines.
- Waterless Processing: Dry screening solutions for arid regions.
Introduction to Iron Ore Crushing
Iron ore is a critical raw material for steel production, and efficient processing requires robust crushing equipment to handle its hardness and abrasiveness. Liming Heavy Industry, a global leader in crushing and screening technology, offers tailored iron ore stone crushing lines that maximize productivity while minimizing operational costs. This article explores Liming’s innovative solutions for iron ore processing, from primary crushing to final product grading.
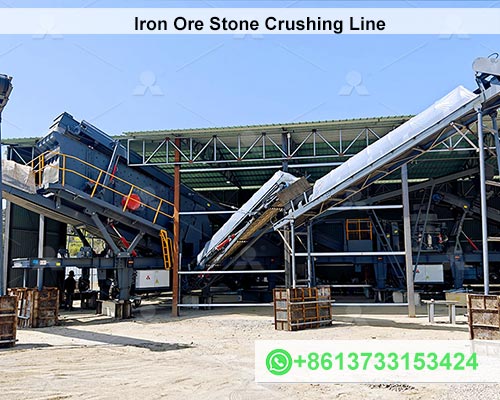
Key Components of an Iron Ore Crushing Line
A well-designed iron ore crushing line by Liming Heavy Industry includes:
Why Choose Liming Heavy Industry for Iron Ore Crushing?
Typical Iron Ore Crushing Process Flow
Cost Optimization Strategies
Case Study: Liming Crushing Line Boosts Output in Australian Mine
A magnetite mine in Western Australia upgraded to a Liming HST Single Cylinder Hydraulic Cone Crusher and S5X Vibrating Screen, achieving:
Future Trends in Iron Ore Crushing
Conclusion
Liming Heavy Industry’s iron ore crushing lines combine cutting-edge technology, durability, and cost efficiency to meet the demands of modern mining. By partnering with Liming, operators gain reliable equipment, expert engineering support, and sustainable solutions that maximize ROI across the ore processing lifecycle.